Supply shortages and an inflexible market give rise to high power transformer lead times
Transformers are a key component in large-scale renewables projects. However, high lead times and rising manufacturing costs are at risk of causing expensive project delays and preventing power plants from being brought online
3 minute read
Kevin Jacobs
Director, Supply Chain Consulting
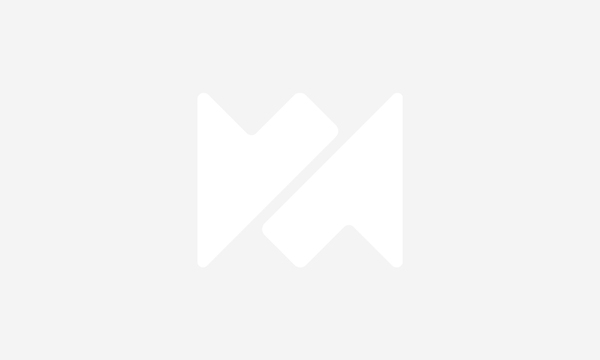
Kevin Jacobs
Director, Supply Chain Consulting
Kevin is a supply chain professional and electrical engineer with extensive experience in the energy sector.
Latest articles by Kevin
View Kevin Jacobs 's full profileSagar Chopra
Senior Research Analyst, Solar
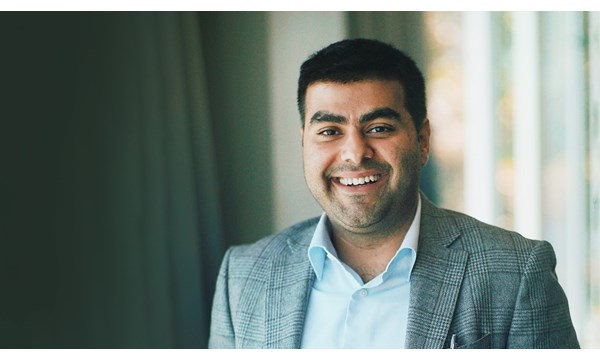
Sagar Chopra
Senior Research Analyst, Solar
Sagar focuses on PV system pricing for US and LATAM regions.
Latest articles by Sagar
-
Opinion
Supply shortages and an inflexible market give rise to high power transformer lead times
-
Opinion
Top 10 solar PV inverter vendors cornered 86% of the market in 2022
-
Featured
Brighter skies for US solar in 2023? | 2023 outlook
-
Opinion
Is the end of high US solar system prices in sight?
Aaron Barr
Global Head, Onshore Wind Energy Research
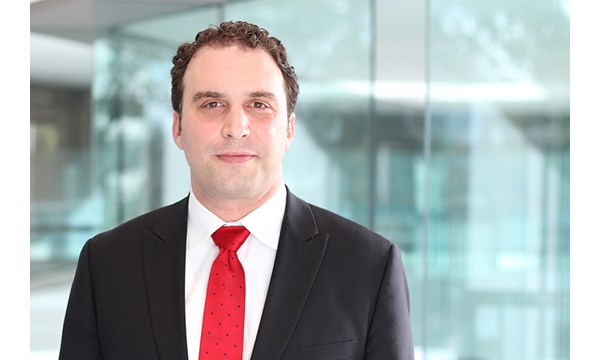
Aaron Barr
Global Head, Onshore Wind Energy Research
Latest articles by Aaron
-
Opinion
EU wind pledges: a little overblown?
-
Featured
Wind 2024 outlook
-
Opinion
Onshore wind energy: what to look for in 2024
-
Opinion
Supply shortages and an inflexible market give rise to high power transformer lead times
-
Opinion
IRA set to increase cumulative US wind energy installations by over 50% in the next five years
-
Opinion
The Inflation Reduction Act and its impact so far
Benjamin Boucher
Senior Analyst
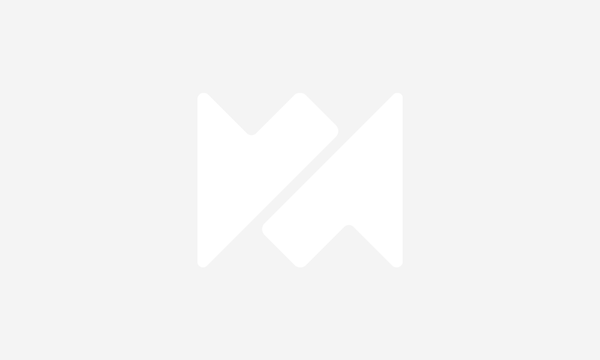
Benjamin Boucher
Senior Analyst
Ben is focused on supply chain research within the utility and renewables space.
Latest articles by Benjamin
View Benjamin Boucher's full profileOur recent report, ‘Supply shortage and high lead times: market dynamics and supply chain update’, explores transformer market dynamics and the factors driving supply shortages. Drawing on proprietary data, insights from research analysts, and deep industry links, we look to understand the transformer sector in greater detail, revealing the reasons behind the increase in lead times, and the rise in component costs.
Fill out the form on the top right to download an extract from the full report, or read on for an introduction to the challenges and opportunities across the sector.
Transformer replacement programmes underway at power plants
Transformer lead times have been increasing for the last 2 years - from 115 weeks in 2021, to 130 weeks on average in 2023.
Large transformers, both substation power, and generator step-up (GSU) transformers, have lead times ranging from 80 to 210 weeks, and some manufacturers have already announced plans to expand capacity to meet growing demand.
As the global installed base of power transformers continues to age, active replacements are underway at most utilities. In the US, a multi-decade replacement programme is underway as installed transformers surpass their 35 to 40-year design life.
In addition to the supply chain imbalance brought about by the pandemic, transformer lead times have also increased because components require custom specifications that can only be provided by specialist manufacturers.
Manufacturers risk financial instability
Given that it can take decades for transformer manufacturers to break even, many are reluctant to make the investments required to expand production. The same manufacturers that acquired the technology and financial capital in the 1980s, are enjoying full production slots and higher margins because of increased global demand. In turn, this limits their motivation to expand and risk financial instability.
Likewise, major original equipment manufacturers (OEMs) continue to cite material, equipment, and skilled labor constraints as driving factors for supply constraints and consequent increased lead times.
In the US, only around 20% of transformer demand can be met by domestic supply. Despite President Biden signing executive orders In June 2022 to help domestic manufacturers increase their production, funding has yet to be specified in any subsequent bills.
Raw material costs doubled
Transformer prices have risen 60% to 70% on average since January 2020. Commodity prices for raw materials such as Grain Oriented Electrical Steel (GOES) have doubled since January 2020, and copper prices have increased approximately 50% over the same time frame.
During the pandemic, manufacturers expected a drop in demand for transformers, and production for these commodities slowed down. As a result, manufacturers are now struggling to ramp up production levels to meet global demand.
GOES prices have surged by more than 125% since January 2020 due to a large market deficit and key manufacturers curtailing production. This has resulted in GSU transformers seeing a 4% to 15% increase in exposure to GOES over the same period.
GOES prices eased considerably in 2023, falling 23% between January and August. However, prices reversed in September, increasing by 24% month-over-month amid better-than-expected macroeconomic indicators in China. Overall, GOES and copper prices eased by 4% and 8% respectively in 2023.
Potential delays to global renewables projects
As utility companies and project developers face transformer shortages, manufacturing players like Virginia Transformer Corporation and WEG have opened new manufacturing plants to increase their production capacity. Likewise, Sunbelt Solomon has made an investment to establish facilities that support the repair and recycling of transformers.
However, based on conversations with developers and suppliers, we predict that as much as 25% of global renewable projects could be at risk of project delays due to high transformer lead times.
The global demand for standalone photovoltaic (PV), wind and grid scale storage are all expected to grow, which will continue to put pressure on lead times. Unless adequate project planning is put in place to account for supply shortages, many projects could end up being delayed.
Learn more
To learn more about the challenges and opportunities in the power transformer market, fill out the form at the top right of the page to download your complimentary extract from the report.
Our detailed coverage of the transformer market can help guide your investment decisions and corporate strategy, while helping you identify the primary drivers that are influencing trade and price dynamics.
You can also find out more about our Supply Chain Intelligence offering here.