PPE is giving the fibres industry some protection from coronavirus
Many fibre, fabric and apparel producers have pivoted to make PPE – but the demand surge won’t last forever
1 minute read
Rob Gilfillan
Head of Polymer & Fibres
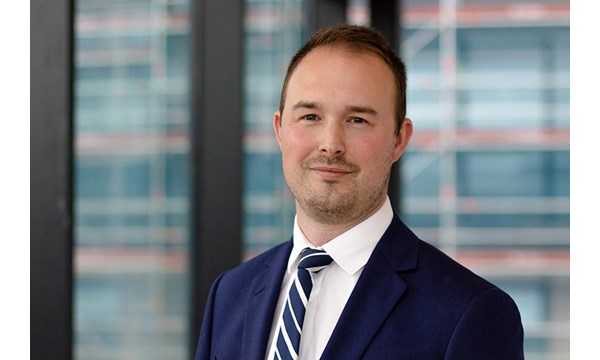
Rob Gilfillan
Head of Polymer & Fibres
Rob leads our research into regional and global markets for fibres, films and flexible packaging.
Latest articles by Rob
-
Featured
Oils & chemicals 2025 outlook
-
Opinion
Plastic demand could reduce by up to 30% in an accelerated energy transition scenario
-
Opinion
Plastic demand: sectoral overview
-
Opinion
The future of automotive industry polymer demand
-
Opinion
Polymer demand scenarios: a little more conversation, a little less plastic
-
Featured
Global challenges weigh on downstream chemical markets in 2023
The fibres industry has seen significant demand destruction from the coronavirus pandemic. Many fibre producers have lowered operating rates to 50% or less, as demand from the downstream textile chain has evaporated. But not all fibre sectors are struggling.
Globally, the need for personal protective equipment (PPE) has boomed. Many fibre and textile companies are pivoting to make PPE, either with existing or newly purchased equipment. Suddenly PPE is not only protecting the people who use it – it’s also providing a lifeline to fibre production.
This article is an excerpt from a recent edition of our regular coronavirus and polymers updates. Fill in the form for a complimentary copy, or read on for some of the highlights.
Coronavirus dealt fibres a heavy blow
All three segments of fibre demand – apparel, household, and industrial – have been hit by the coronavirus pandemic. That’s significant up the chain, as fibres represent 64% of polyester polymer demand.
The destruction has been rapid and extensive. Stringent quarantine measures around the world have disrupted downstream textile activity, from apparel production to auto component manufacturing, and dragged down end-user demand. And it could be a long road to recovery.
Textile and apparel industries face a huge challenge
Many textile and apparel brands and retailers have cancelled or delayed orders, but many will need exceptional marketing and supply chain management skills to avoid being left with unwanted inventory.
Heavy discounting is likely – though in the current economic climate consumers will focus purchasing decisions more on needs than wants. And while discounts may help in the short term, the margin destruction will add to the stresses already apparent in a disrupted supply chain.
Loyalty may help cushion some companies during the crisis. Some leading apparel companies have expressed commitments to support suppliers, by honouring existing contracts or helping manufacturers in poorer countries. But several large brands are also filing for bankruptcy, closing stores or closing down altogether. The impact on employees, shareholders and suppliers can’t be cushioned.
PPE demand has provided a welcome boost to fibres
PPE demand has helped to offset some of the demand destruction. The uplift in demand for fibre-grade polypropylene (PP) for mask production has been significant, to say the least. Last year, China’s daily mask production was 20 million units. During February that increased to around 150 million units. Based on a conversion rate of one tonne of PP to 250,000 units of N95 masks, that level of output required 600 tonnes of fibre-grade PP each day.
That hasn’t been easy to deliver. The main bottleneck in February was the mid-layer, made from meltblown PP nonwoven product. It takes time and investment to expand production capacity – normally three to four months for a local machine and six to eight months for an import, at a cost of around RMB8-10 million.
Producers pivoted to meet PPE demand
In early April the situation changed. Some textile machinery manufacturers claimed they could supply meltblown fabric machines by updating normal nonwoven lines, at a much lower price of RMB 300,000 and a turnaround of only three to four days. Many plants invested and began making meltblown fabric.
We estimate that around 10 kilotonnes of PP per day was needed to supply those low-quality meltblown plants, around 16 times more than the original 600 tonnes per day.
The PPE demand boost extends to multiple fibres
It’s not just polypropylene in China that has been in hot demand. In Europe, producers of polyester staple fibre (PSF) had a welcome boost from PPE and the broader hygiene sector. This has helped to offset the fact that production for the automotive sector ground almost to a standstill.
Other fibres are also seeing the benefit of the surge in demand for PPE. While most mask ear loops use polyester and spandex as the raw material, nylon is also being used for some high-quality product, and is the preferred choice for the N95 mask.
To read more about the demand boost and price impact for PP, spandex and nylon, fill in the form on this page to read the insight in full.
Looking beyond the current crisis
Coronavirus is still an unfolding story. We expect that some of the many fibre, fabric, and apparel producers that have pivoted to making PPE will continue with this effort, post-pandemic. And we are confident that they will continue to perform an essential function as the world emerges from this crisis.
But the current PPE surge will not continue forever. Hospitals and governments will restock emergency supplies. Demand will drop as the world returns to ‘normal’ – though it’s not yet clear what the new normal will look like.
We do know that it will take some time for consumer confidence to restore apparel purchasing to pre-coronavirus levels. And this will only happen after the workforce returns in great numbers and the economy starts to recover. The question is, how many companies can survive in the meantime?
To read this insight in full, fill in the form at the top of this page for a complimentary copy of 'Coronavirus and polymers – are fibre markets spinning out?'
Stay up to date with the global fibres industry
Our Fibres Global Monthly Market Overview provides a detailed overview of the industry, supported by robust proprietary data. This includes regular information on key events, supply and demand balances, prices and analysis of global and regional market trends.
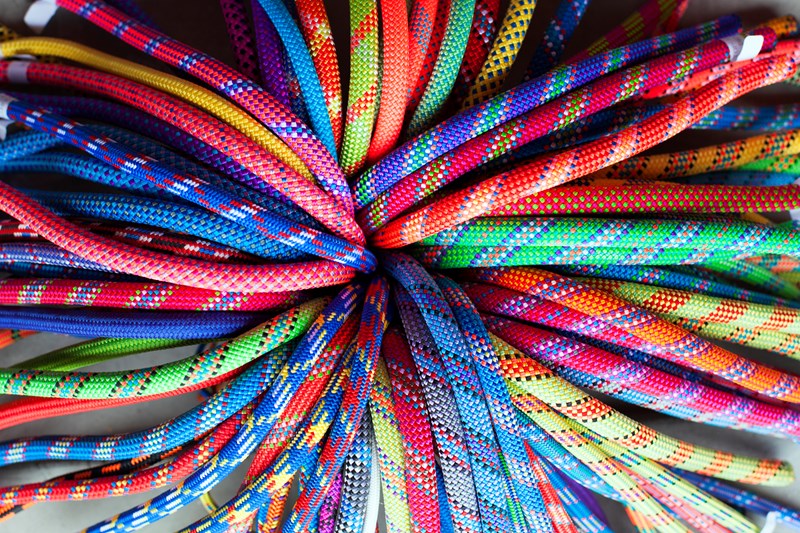