Is green aluminium an achievable goal?
Assessing cradle-to-gate emissions and the path to decarbonisation
1 minute read
By James Whiteside, Research Director, Global Head of Multi-Commodity Research and Edgardo Gelsomino, Head of Aluminium Research.
Metals producers face a dual challenge in the energy transition. They must meet rising global demand for crucial commodities while also cutting emissions. For aluminium the challenge is greater – of all the metals, it faces the biggest impact from carbon pricing. But how significant is the risk? And is carbon neutral aluminium achievable?
We discussed this topic in detail in a recent webinar: ‘What is the true carbon footprint of the metals we produce?’ Got 25 minutes? Fill in the form for a complimentary replay, and a copy of the presentation slides and charts. Got five minutes? Read on for four green aluminium FAQs.
How significant is carbon policy risk for aluminium?
To meet the requirements of the Paris Agreement, direct emissions from metals production must halve over the next 20 years. Carbon pricing will be vital, but, to date, of the 189 signatories to the Paris Agreement only 58 jurisdictions have implemented such a regime.
Our view is that the global price of carbon dioxide per tonne must rise to US$110 by 2030 in order to keep global warming below 2 degrees. This would radically change the production economics of emissive industries, like metals production, and spark significant technological change.
Among metals, aluminium produces the second-highest absolute emissions (2% of the global total – second only to steel) and competes with nickel for highest intensity. It stands to be the metal most affected by carbon pricing as a result.
How would a global carbon tax affect aluminium economics? Watch the webinar replay for a discussion of how the cost curve changes under three carbon cost scenarios.
How can stakeholders benchmark carbon emissions?
As carbon policy evolves, all industry stakeholders are becoming acutely aware of the risk. A competitive advantage could be won or lost on this battlefield. But corporate disclosures aren’t enough to understand the full impact – the metrics aren’t consistent, and there isn’t always sufficient detail on the sources and drivers.
At Wood Mackenzie, we’ve developed an emissions benchmarking tool that assesses cradle-to-gate emissions, from raw materials extraction all the way to the cast house gate. This gives us an holistic view of the carbon footprint of aluminium production – and how producers might reduce it.
Contact us to find out more about the emissions benchmarking tool.
Is any aluminium green today?
In a word, no. When the entire value chain is considered, no aluminium is currently carbon neutral. Our research shows that cradle-to-gate C02 equivalent emissions range from 5-25 tonnes per tonne of metal produced.
The chart below gives a good indication of where those emissions typically come from – and how much it can vary between assets. This anonymised example shows a European hydro-powered smelter that sources alumina from the Atlantic market compared to an integrated, coal-powered operation in India that sources alumina domestically. The latter’s emissions are more than three times higher.
While raw material sourcing does have a material impact, the primary driver of emissions in aluminium production is the energy source.
To hear the full discussion of emissions in mines, alumina refineries and smelters, fill in the form to watch the webinar replay.
How can the aluminium industry go green?
There is a path to complete decarbonisation (or carbon-neutral metal) – but it’s a long and challenging one.
Reducing the industry’s heavy reliance on fossil fuels is the biggest factor. Policies that penalise metals produced from high-carbon sources will be necessary to spark real change – and it will take time to see the impact.
Increased recycling will also be key, as production of aluminium from scrap takes only 5% of the energy required to smelt alumina. But while miners will face more competition from scrap they will still play an important role. Not all applications can use scrap as feed, and there simply isn’t enough metal in circulation to meet global demand.
Technological innovation will be crucial. The aluminium industry must invest in up-scaling carbon anode replacement technology to reduce emissions from electrolytic cells.
Supply chain localisation will also contribute to greener aluminium. Reducing freight emissions and migrating smelting to locations with renewable energy sources may be necessary in the long term.
How much CO2 per tonne of metal could each of these measures displace? Watch the webinar replay for our assessment. This also includes:
- How a global carbon tax would shift smelting economics
- Case study: how a change in raw material sources affected one Canadian smelter’s carbon footprint
- Presentation slides, including charts.
Fill in the form at the top of the page for complimentary access.
Get in touch
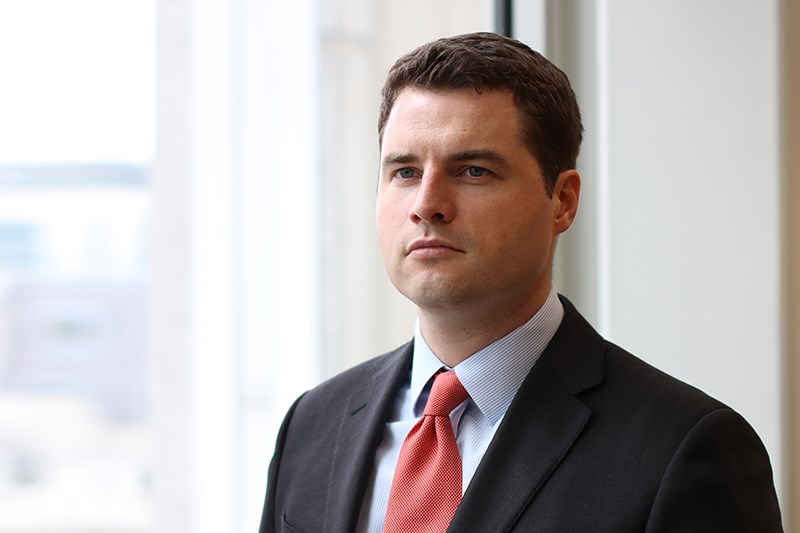
James Whiteside, Research Director, Global Head of Multi-Commodity Research