Our product portfolio
Explore our solutions covering the entire renewables, energy and natural resources supply chain
Our product portfolio
Explore our solutions covering the entire renewables, energy and natural resources supply chain
Clarity where you need it most
Across our product portfolio, we provide market-leading insights into the assets, markets and companies at the heart of the energy transition.
Assets
Assets
Whether you’re valuing an existing asset or weighing up a new acquisition or build, data accuracy is everything. Our analysts meticulously source and connect reliable datapoints across commodities to give you a true picture of your target assets. That’s why major organisations, banks and governments refuse to invest without our insights.
Markets
Markets
Energy and natural resources markets have never been more connected or chaotic. To help you understand what’s really going on, our market analysis is driven by the deepest, broadest and most accurate data across interconnected industries – giving you the power to forecast and capitalise on future market movements.
Companies
Companies
If you’re benchmarking the competition or looking for ways to beat them, you need a clear view of the competitive landscape. Our unbiased analysis brings the strategies, market sentiment and financial health of leading companies into focus. Giving you an expert eye on the boardroom decisions of every major player in your market.
Our consulting services
Turn insight into impact with independent advice and guidance. Our expert consultants add a new dimension to our data and analytics, helping you navigate critical challenges and execute capital investment decisions with confidence.
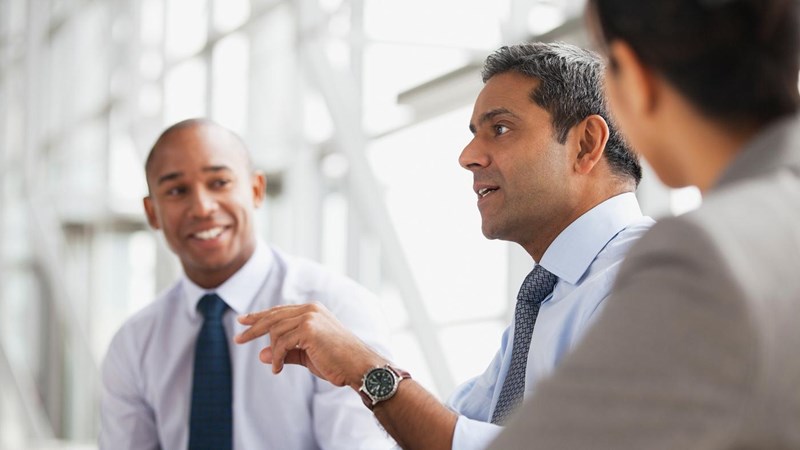