Can recycling fill the battery raw material supply gap?
Battery recycling will play a key role in meeting energy transition demand – but it is beset by challenges
1 minute read
Batteries are a critical component of the energy transition. As electric vehicle (EV) sales continue to accelerate, demand for Lithium-ion (Li-on) batteries will hit nearly 3 TWh by 2030. But as demand booms, a battery raw material supply gap looms. Can recycling fill it?
I explored this topic in detail at the recent Advanced Automotive Battery Conference, drawing on insight from our Battery & Raw Materials Service. Fill in the form for a complimentary copy of my presentation slides, and read on for an overview.
Demand for batteries will put huge pressure on raw material supply
Li-ion is currently the battery of choice for EVs and energy storage systems (ESS). This can be attributed to the maturity of the technology – helped by the portable electronics sector – combined with unrivalled energy and power capabilities.
Right now, EVs are the dominant sector for battery demand. We forecast that 30 million EVs will be sold in 2030, representing 30% of global passenger car sales. By 2040, they’ll account for 52%. Battery supply chains will come under growing pressure as a result. Demand for raw materials, such as lithium, cobalt and nickel, is set to grow at a rate that outstrips supply.
Expanding supply of critical battery raw materials won’t be easy
Traditional routes to adapt to increased demand are unlikely to cope with the current ramp-up:
- Battery innovation can take many years from discovery to commercialisation – especially on the scale needed to meet EV demand.
- Increasing mine supply can take up to 10 years from exploration to production.
- Reducing battery demand through EV design evolution – for instance, the development of swappable batteries – requires multiple model iterations.
There’s no quick fix via these routes, certainly not one that can keep pace with the unprecedented, change we’re seeing now – a societal overhaul, rather than a gradual transition to competing technology.
Recycling can play an important role in meeting battery demand
There is a huge role for recycling in the transition to a more sustainable world, to both eliminate waste and reduce the need for rapid expansion in carbon-intensive mines.
Together, recycling production scrap and end-of-life batteries could become a substantial source of raw material to meet surging demand. It also presents an opportunity to source materials in regions that lack natural resources.
However, the collection and recycling of end-of-life batteries is beset by challenges. Firstly, when the cathode containing the critical metals is installed into an EV, the metal is severely diluted by pack materials like casings, interconnects and cooling channels. Recycling is not a straightforward process, and the value of an EV pack is much less than the value of cathode material of the same kWh.
Secondly, end-of-life feedstock is substantial but recyclers will have to wait for it. EV packs have long warranties. The top automakers provide at least an eight-year warranty on battery packs, and expect a much longer lifespan. In addition, the emergence of second-use applications, like residential or industrial energy storage, will also keep EVs from entering the recycling system.
Manufacturing scrap will be the main source of recycled battery material this decade
China, Europe and North America will see huge increases in battery and cathode manufacturing to meet demand.
This is a significant opportunity for production scrap, especially as new players and new facilities continue to enter the market. Even experienced cell manufacturers can see a significant portion of cells produced become waste before entering end-use applications.
Recycling alone cannot meet battery raw material demand
While recycling can ease the pressure of supply deficits, it won’t match demand. The amount of production scrap or EVs coming to end of life simply can’t keep pace with EV and ESS growth. A push in expanding supply of virgin materials while maximising the recycling sector to ease the deficit will be necessary.
Recyclers will need to be adaptable. Automakers and cell manufacturers will naturally look to lower cost materials. This could include increasing use of lithium iron phosphate (LFP) batteries and a decreased cobalt content in nickel -manganese-cobalt (NMC) batteries, as well as penetration of sodium-ion (Na-ion) technology to the market. Such changes would impact production scrap recycling margins, and require changes in recycling processes.
Ultimately, increased recycling is crucial. But it may need to be driven by policy rather than economics.
To find out more about battery recycling, download the presentation for charts on:
- Global cathode demand and quantity reaching end of life
- Regional cathode manufacturing capacity
- Global cathode demand by tonnes
- And more
Fill in the form at the top of the page for your copy.
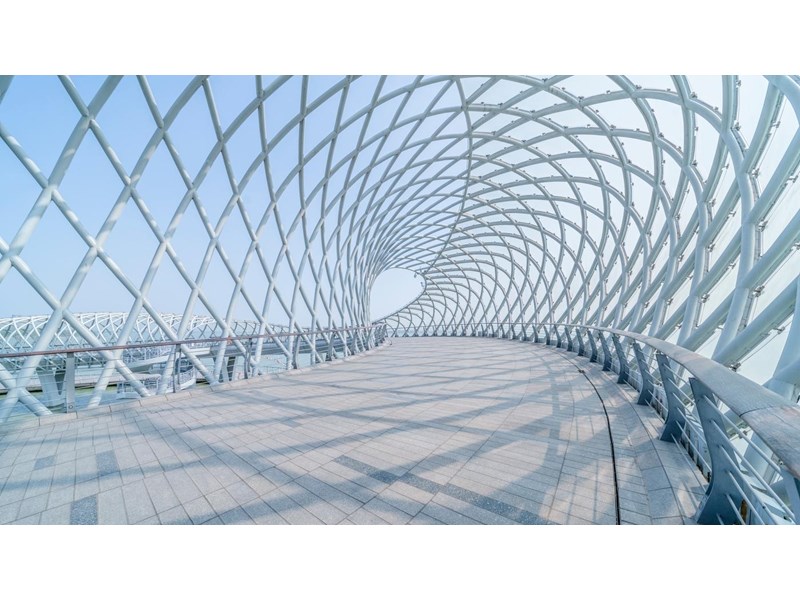