Discuss your challenges with our solutions experts
1 minute read
By Julian Kettle, Vice-Chair Metals and Mining, and Renate Featherstone, Principal Analyst, Multi-Commodity Research
We have extracted metals from the earth’s crust for millennia. We’ve converted mined material into primary metal at considerable financial and environmental cost. And yet we only recycle a fraction of the metal that we extract – despite the fact that most can be reused infinitely. Could increased recycling displace our need for freshly mined metal and help save the planet for future generations? Is there enough scrap metal in the system to satiate humankind’s endless demand for more?
Governments are reluctant to put the environment before economic growth but, increasingly, the two will be interlinked. A strong economic rationale exists for greater scrap processing and use. Capital investment costs for scrap processing facilities for aluminium are typically 10% of that for primary and 50% or less for steel. Then there are the carbon emissions benefits – typically, secondary aluminium production has a carbon footprint five to 25 times lower than primary metal production. For steel, the largest industrial emitter, emissions can be halved.
Although scrap demand will outpace growth for primary metal, it will remain underutilised compared to its overall availability. Why? Because price, profit, quality and technological considerations currently drive development of the secondary industry. But stricter environmental policies will change scrap availability and use.
The prospect of a US$110/tonne carbon price will undoubtedly lead to an acceleration of scrap processing in carbon-intensive industries.
One example would be carbon tax policy. The prospect of a US$110/tonne carbon price (Wood Mackenzie’s estimated global carbon price required to limit warming to 2 degrees) will undoubtedly lead to an acceleration of scrap processing in carbon-intensive industries. In contrast, for low carbon-intensive industries, untouched by carbon taxes, uptake in scrap use is likely to be slower and will depend heavily on relative production costs.
Consumer and investor pressures – demanding recycled content – could transform the market but it will not happen until incentives are compelling and quality can be maintained. Policies that mandate greater recycling rates are already driving cleaner and more reusable scrap collection. Furthermore, policies on minimum recycled content could spur demand for scrap. In addition, we believe that governments will increasingly see scrap as a strategic source of low-carbon domestic supply with significant growth potential.
If policy is the key to unlocking scrap availability, how much metal scrap could be recovered? And if all available scrap is recovered will we need to mine metals in the future?
It’s impossible to eliminate the need for the mining and processing of primary metal, even allowing for a massive expansion of scrap availability. Many end uses cannot use scrap while rising demand for metal elsewhere will mean that scrap alone couldn’t fill the gap. Absent seismic shifts in policy and society, scrap will remain underutilised.
Environmental policy will force a rapid increase in scrap utilisation. By 2040, an extreme environmental regulation scenario equivalent to our AET-2, or 2 °C world scenario, would reduce primary metal demand by up to 35% for iron, 47% for aluminium and 34% for copper. This could prove truly transformative for producers and the planet alike.
The art of estimating scrap availability
We first need to establish levels of scrap availability. This is defined as an unconstrained view of scrap supply potential – a scenario where metal prices, consumer demand and scrap quality don’t matter. In the real world, of course, these considerations can’t be ignored so scrap availability offers a view of the maximum potential supply.
There are two types of scrap: scrap generated through production processes – semifabricator and fabricator scrap – and scrap recovered from end-of-life goods (old scrap). Calculations of scrap availability depend on five assumptions, which vary for different metals, products, years and countries:
- semi-fabrication yield loss
- fabrication yield loss
- lifecycle assessment
- collection rates
- recyclability rates.
To illustrate the global scrap story, take the humble laptop. It contains an average of around 20g of steel, 40g of aluminium and 140g of copper. Some material is lost in the metal and then the laptop production processes, contributing to semi-fabricator (1) and fabricator (2) scrap. What’s more, because of policy considerations, your laptop is already designed with its recyclability (5) in mind.
There are two key aspects to scrap modelling, which will influence global scrap availability: individuals’ choices – how long you keep your laptop and how you dispose of it – and the overall trend that emerges from all these choices.
(3) Life cycle. There is huge variability in the useable life of a product. Our rule of thumb is that there is a 60% chance you will dispose of your laptop when it is between three and seven years old, and that you won’t keep it beyond 10 years.
(4) Collection rates. Choices for disposal in many countries are largely determined by government policy. In Europe, for example, the new Waste Electric and Electronic Equipment (WEEE) Regulations dictate that 65% of electronic equipment sold must be collected and presented for recycling. Consumers are now routinely offered discounts on a new laptop if they bring in their old one for recycling. Producers,
distributors and electronic equipment retailers are incentivised to get your old laptop back to meet the WEEE Regulation targets.
Future collection rates are the most significant drivers for scrap availability and are determined by government policy. In turn, this is heavily influenced by environmental
concerns.
We believe end-of-life product collection rates will rise moderately by some five percentage points over the next two decades on the back of future environmental policy.
Purchasing and disposal choices drive scrap supply
When it comes to your laptop’s disposal, we can capture consumer choices through lifecycle distribution and different scrap collection rates. However, given the millions of products that use metals and the myriad product lifecycles, we must make some broad assumptions and condense the numbers of products and sectors we model.
In other words, to make the analysis manageable, we simplify the world of scrap generation.
Reality check: not all scrap can be consumed
Solid waste laws and regulations govern scrap collection rates and these differ across the world. In Europe, policies are more advanced and are set out for hazardous waste, vehicles, waste electronics and ships. In the US, by contrast, policies differ by state. In China, a new scrap import regulation encourages domestic scrap collection. In India, the government plans to introduce a vehicle scrappage policy.
What all these policies share is a focus on keeping reusable materials out of landfill. They should, in theory, lead to greater scrap availability and use. However, there are no universal laws that encourage the consumption of recycled materials.
For example, Europe – which collects scrap – does not have enough scrap-smelting capacity to use all of the scrap generated. Consequently, vast quantities of scrap are exported. Unverifiable quality for end-of-life scrap has deterred higher scrap use. But solid waste management laws are tightening, leading to increased scrap separation and quality monitoring. It’s now easier to purchase clean end-of-life scrap than it has been at any point in our lifetimes.
Furthermore, scrap use will rise when policies and laws start to focus on the recycled content in consumer goods. But this won’t happen overnight. The long lead times for systems and processes can’t be fast tracked. After all, solid waste regulations have been evolving since the 1992 Basel Convention. Three decades on, solid waste policy implementation is still far from universal. We don’t yet live in an entirely scrap ‘woke’ world. The speed at which we get there will differ significantly between carbon-intensive and low carbon-intensive industries.
We estimate that using all available scrap could bring down aluminium and steelmaking emissions by up to 600 Mt a year each.
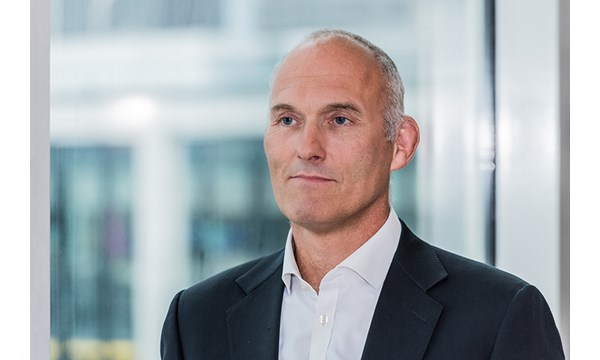
In carbon-intensive steel and aluminium, there are non-price related incentives to use scrap. Scrap can help lower emissions significantly. Typically, secondary aluminium production has a carbon footprint five to 25 times lower than primary metal production. For steel, the largest industrial emitter, increased scrap use could halve emissions. We estimate that using all available scrap could bring down aluminium and steelmaking emissions by up to 600 Mt a year each. If a universal carbon price rises to S$110/tonne, each relevant industry could save US$66 billion a year – a huge incentive for increased scrap use.
However, even across these carbon-intensive industries the approach will be producer-specific. In the Nordic countries, widely recognised as more focused on sustainability, you can find contrary examples on scrap-use strategies. Norwegian producer Hydro Aluminium has increased its exposure to scrap metal alongside its predominantly hydro-powered primary production. In contrast, just over the border in Sweden, a steel producer has turned to new capital-intensive, hydrogen-based carbon-free iron making, rather than scrap. Yet Sweden still exports scrap that it could consume. The rationale is that scrap-based steelmaking cannot meet required quality standards. Fundamentally, the increase in scrap consumption will be unequal across industries and countries.
The rise in scrap use will be even less pronounced in less carbon-intensive industries, like copper. Here price considerations determine scrap use in the short term. In the longer term, policy-driven improvements in closed-loop recycling and scrap segregation will enable cleaner scrap availability. However, there is little immediate incentive to increase scrap consumption, even if it is becomes theoretically available.
Even with increased scrap availability, scrap cannot eliminate the need for primary metal. Mining, refining and smelting will remain part of our lives for many decades to come.
Can scrap fill the gap?
In the current political landscape and faced with evolving societal attitudes about the environment, we likely won’t use all the available scrap – we simply aren’t incentivised to. Our steel base case assumes the status quo evolves, with an additional 200 Mt/a of steel scrap used by 2040. This means 80 Mt/a of new iron units will still be required to meet demand – yet there is already more than enough scrap in the system to meet this additional demand. The potential risk to growth in mining is huge.
Similarly, for aluminium, additional demand for primary metal to 2040 could be half of our base case forecast of 75 Mt/a. Meanwhile, for copper, the additional demand growth that the energy transition requires could be wholly met by increased collection and use of scrap rather than the development of new mine supply. In theory!
Policy-driven improvements in closed-loop recycling and scrap segregation will enable higher scrap utilisation. Furthermore, carbon policy is a driving force for change – when it comes, we’ll see an inevitable restructuring of the carbon-intensive steel and aluminium industries with scrap playing a starring role. Nevertheless, we will still need to mine for metal but we can at least see how to meet our almost insatiable demand while remaining at today’s level of mining. Scrap certainly can fill part of the supply gap – but not all.