4 years into a difficult transformers market in the US, is there a potential end in sight?
Amid surging demand and supply constraints, find out how new policies and industry expansions are shaping the future of the US transformers market
5 minute read
Isabel Schwartz
Vice President, Supply Chain Consulting
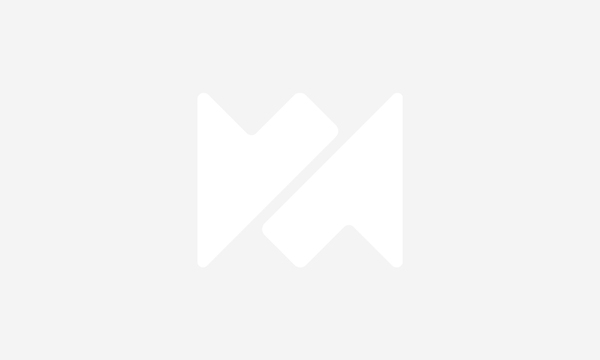
Isabel Schwartz
Vice President, Supply Chain Consulting
Isabel is a leader in the supply chain consulting practice.
Latest articles by Isabel
-
Opinion
Supply chain call to action: navigating tariff uncertainty today
-
Opinion
Navigating the impact of President Trump's tariffs on utility supply chains
-
Opinion
4 years into a difficult transformers market in the US, is there a potential end in sight?
-
Opinion
Supplier diversity programs: a new source of competitiveness and innovation for utilities in North America?
Kevin Jacobs
Director, Supply Chain Consulting
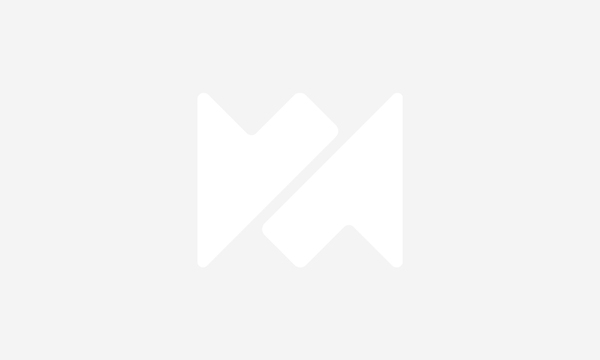
Kevin Jacobs
Director, Supply Chain Consulting
Kevin is a supply chain professional and electrical engineer with extensive experience in the energy sector.
Latest articles by Kevin
-
Opinion
4 years into a difficult transformers market in the US, is there a potential end in sight?
-
Opinion
Supply shortages and an inflexible market give rise to high power transformer lead times
Transformers are a key component in the existing and new electrical infrastructure needed for the generation and distribution of electric power. As such, they are an irreplaceable piece of equipment in most generating facilities and substations. Several key policies (IRA, CHIPS, IIJA) and decade-long trends (Electrification, Grid Hardening Reliability Investments, Load Growth) have led to a significant increase in demand for transformers in the US over the past few years.
Supply has struggled to keep pace with demand as the market, particularly for power and GSU transformers, has a limited supplier pool due to the high capital cost barrier to entry for manufacturing transformers. However, the recent Department of Energy (DoE) ruling on energy efficiency standards for distribution transformers and announced expansion investments across OEMs represent a bright spot in a market that has been in turmoil for the past few years.
Fill in the form at the top of the page to download our full report, or read on for some of the key messages from the analysis.
What is the current state of transformer availability in the US?
Lead times for transformers have been increasing significantly since the pandemic as a result of demand outpacing supply. Lead times for power and GSU transformers have tripled since 2021, reaching an average of ~150 weeks after receipt of order (ARO) over the last two quarters, with larger transformers driving the higher end of lead times. Lead times for distribution padmount transformers have also increased significantly over the last two quarters, reaching ~75 weeks ARO on average. Conversely, lead times for pole-top transformers have started to ease - many utilities stockpiled pole-top transformers through 2022 and 2023, which has greatly lessened the demand on pole-top manufacturers and allowed them to bring down lead times for those production lines.
From a cost perspective, there has been an observed divergence in transformer cost trends. Historically, these cost trends were primarily driven by the transformer’s core commodities – e.g., Steel and Copper. However, as demand has increased beyond supply capacity, it has become a supplier’s market, and supplier margin now makes up an increasingly larger portion of total cost.
Wood Mackenzie has observed a 4x increase in margins across power transformers and nearly a 5x increase in margins across distribution transformers since 2020. Margins now make up ~20% of the overall unit cost of transformers. Even as pricing for steel and copper has stabilised, the pricing for transformers has remained high after seeing a 70-75%+ rise since 2020. Costs may be elevated for the foreseeable future until new supply comes online.
How will the recent DoE ruling on energy efficiency standards for distribution transformers impact the market?
The DoE issued its final distribution transformers efficiency ruling in April 2024. After facing significant backlash on its initially proposed ruling that would have required a major shift in the fundamental inputs to transformers to meet the proposed requirements, the final DoE ruling reflects a middle-ground approach that balances efficiency goals with the realities of the transformer industry.
The finalised ruling will allow a majority (75%) of the market to continue utilising industry-standard GOES (Grain Oriented Electrical Steel) to meet the new efficiency requirements; analysis of the initial proposed plan found that nearly 95% of transformers would have had to shift to using amorphous steel cores.
This was particularly alarming as GOES and Amorphous production lines are not interchangeable. All new amorphous production capacity would have needed to be built (vs. a retooling of existing capacity), adding a significant cost to each manufacturer and requiring multiple years for the production ramp-up and engineering re-design of thousands of transformers. Given that the market is dominated by GOES, the updated ruling helps mitigate additional pressure on an already stressed supply market.
Although the industry breathed a brief sigh of relief when the final ruling was announced, there is still work to be done to meet the new requirements and constraints that Owners need to be mindful of. For example, there is only one producer of GOES for transformers in North America, Cleveland Cliffs, and the National Renewable Energy Laboratory (NREL) estimates a tripling in installations on transformers by 2050. Therefore, supply constraints could still be seen due to overall demand increase over time.
Additionally, Owners and Manufacturers will need to review the design of existing SKUs to understand if they fall within the scope of this ruling and, if so, the ruling’s impacts on design. Impacts may be minor if the design can still utilise GOES or they may be major if a switch to Amorphous steel is required.
How are suppliers and Owners reacting to the current state of the market?
The challenge to secure the supply of pole-top transformers over the past few years has resulted in a shift towards international vendors for an alternate supply base as domestic manufacturers struggled to keep pace with demand. It remains to be seen if this trend towards international vendors will be permanent.
On one hand, dependency on foreign vendors increases supply risk. On the other, domestic OEMs still struggle with production capacity and may also have a difficult time competing with international vendor unit costs.
Suppliers continue to remain selective with whom they work but are slowly accepting more low-volume and complex unit orders as part of purchases containing the more lucrative high-volume SKUs. Owners with close manufacturer relationships – those regularly meeting to review demand plans, production capacity, and expectations – have mitigated lead times and supply crunches more effectively.
For example, Owners provide demand commitments to vendors early (years in advance) with high-level characteristics (high/low-side voltage, kVA ratings, etc.) and then meet with manufacturers 16 weeks out from production start to confirm each SKU detail, confirm demand, and mutually agree on updated pricing and lead times, ultimately mitigating surprise and volatility from both parties.
With more certainty in future demand for transformers driven by policies and decade-long trends (e.g., consistently high demand expected for years from the IRA and increased Load Growth) and the longer timeline for standards set by the DoE, suppliers have gained the confidence required to invest in manufacturing expansions. Major OEMs have recently announced acquisitions and plant expansions for both power and distribution transformers – in the US and abroad. These announcements have been a bright spot for a severely constrained market; however, expansions will likely not influence supply until 2025 at the earliest.
In summary, it appears that the market may be easing after a difficult stretch for pole-top transformers, but at least in the next 2 – 3 years, there will likely continue to be constraints for padmounts and larger transformers. With suppliers investing in expansions, we should expect to see supply challenges alleviate across all markets in the mid-term (3 – 5 years) as capacity comes online. However, we are years (5+) away from any return to normal trends.
Learn more
Don’t forget to fill in the form at the top of the page to download the report which includes further analysis and detailed graphs.