Batteries with Chinese characteristics
China’s control of raw materials supply chains risks leaving others standing
3 minute read
Gavin Thompson
Vice Chairman, Energy – Europe, Middle East & Africa
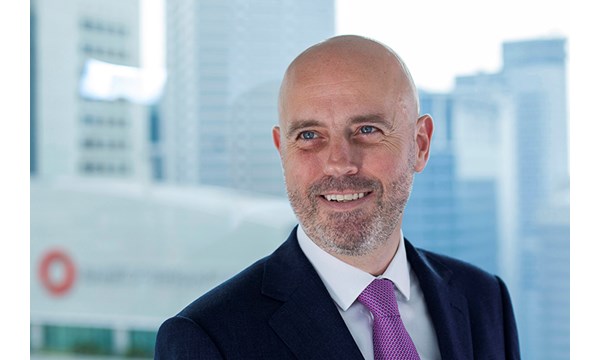
Gavin Thompson
Vice Chairman, Energy – Europe, Middle East & Africa
Gavin oversees our Europe, Middle East and Africa research.
Latest articles by Gavin
-
The Edge
A world first: shipping carbon exports for storage
-
The Edge
WoodMac’s Gas, LNG and the Future of Energy conference: five key themes
-
The Edge
Nigeria’s bold strategy to double oil production
-
The Edge
US tariffs – unpredictability is the strategic planners’ nightmare
-
The Edge
Upside pressure mounts on US gas prices
-
The Edge
The coming geothermal age
A key early goal of President Biden’s ‘Buy American’ policy is a push to replace the federal government’s fleet with American-made electric vehicles (EVs). As this definition requires that a minimum 50% of components are domestically produced, a key focus is now on battery production. As Energy Secretary-elect Jennifer Granholm argued at her recent nomination hearing, “We can buy electric car batteries from Asia or we can make them in America.”
Similar policies are in place in Europe. And while the EU’s current local content threshold is lower for electric vehicles versus internal combustion engine vehicles at 40%, this is intended to rise to a comparable 55% by 2027. As with the US, European governments are encouraging investment in battery factories to replace traditional engine plants, shortening supply chains and keeping domestic car manufacturing alive and well for years to come.
But there’s a major obstacle to achieving this. At present, China accounts for almost 75% of global lithium-ion battery manufacturing capacity and this share is set to increase through the short term with its build-out of new facilities. And although the US and Europe are enacting policies to encourage domestic battery production, there has been a distinct lack of support for investment in the supply and refining of the raw materials to achieve this. In China, the opposite holds true.
To learn more about what this means for the future of battery manufacturing, I spoke to Gavin Montgomery and Milan Thakore from our Battery Raw Materials team.
The metals of mobility
The five heavyweight metals for EV manufacturing are copper, aluminium, nickel, cobalt and lithium. But while the vehicle body relies highly on aluminium to minimise weight and uses copper for wiring, it is the three key cathode battery metals – lithium, nickel and cobalt – that are key to the production of batteries.
The electrification of mobility is central to global efforts to decarbonise. And if the pace of EV production and ownership is to really take off, must be a huge increase in the production and refining of the key metals to achieve this. Wood Mackenzie’s base case sees nickel production rise by almost 70% by 2040, while cobalt and lithium demand will increase by 200% and 600%, respectively, over the next two decades. And if the world decarbonises more rapidly, demand rises far faster.
You might be interested in: Metals & mining: what to look out for in 2021
China’s rising dominance of supply and refining
First things first, China does not have it all its own way in the contest for key metals used in EV production. China remains hugely dependent on foreign miners, for example, for its supply of copper – the country is net short to the tune of around 9 Mtpa – with only limited equity ownership of resources around the world. Just as with iron ore, despite considerable efforts China has struggled to significantly increase its share of global copper resources.
Arguably, this has fuelled China’s determination to seek greater control over battery raw materials supply chains. Over the past decade, the country has taken enormous strides to increase its ownership of, and access to, these, from cobalt resources in the Democratic Republic of Congo (DRC) to lithium reserves in Chile and Indonesian nickel mines.
Cobalt – from the DRC to the PRC
With the country's increasing grip on global supply, Chinese miners are less encumbered than their western peers. Able to access competitive state capital and with lower requirement on returns, Chinese companies also face far less scrutiny on ESG, encouraging more appetite to operate in high-risk areas. Cobalt is a prime example. Almost three-quarters – and rising – of global cobalt production comes from the DRC, where western miners face prohibitive ESG risks. It is no coincidence that China’s cobalt refining capacity almost exactly matches the DRC’s share of global output.
Access to raw materials isn’t the only story. China has also built out the lion’s share of refining capacity for these key battery materials, ensuring greater control over supply chains.
Chinese – and Asian – manufacturers are going global
Even as battery makers around the world look to invest in new capacity, mainland China will still be the largest producer of EV batteries by 2030, accounting for around two-thirds of total base case global manufacturing by this time.
And faced with potential tariff barriers, Chinese companies, as well as other Asian battery manufacturers, are expanding their footprint overseas. China’s SVOLT has now confirmed it will build a 24-GWh plant in Germany, with cell production scheduled to begin in 2022, and module production the following year. In other parts of Europe and the US, South Korean and Japanese battery makers are also building new capacity.
Alternative technologies hold promise, but access to raw materials remains key
While the expansion of China’s battery manufacturing capacity is progressing in parallel with increasing Chinese ownership of the required raw materials and refining capacity, competing battery makers still have options. China’s control over production is far from absolute, while manufacturers are also investing heavily in thrifting to reduce the proportion of cobalt in batteries. General Motors and LG are developing a new battery system using 70% less cobalt through the increased use of aluminium, while Panasonic and Tesla are working on cobalt-free, high energy-density battery technology.
This is encouraging, but even with the potential for a reduction in cobalt per battery, the scale of future EV production increases demand significantly. If global miners, battery producers and EV manufacturers are to compete with China as demand grows, they must also pursue greater investment across the range of raw materials and processing needed for battery production. This will need political support. For governments talking up domestic battery production, an improved understanding of existing raw material supply chains would be a good place to start.
A happy Chinese New Year to you all and best wishes for the Year of the Ox.
APAC Energy Buzz is a weekly blog by Wood Mackenzie Asia Pacific Vice Chair, Gavin Thompson. In his blog, Gavin shares the sights and sounds of what’s trending in the region and what’s weighing on business leaders’ minds.