Discuss your challenges with our solutions experts
Five ways the copper industry can improve economics and sustainability
1 minute read
Driven by a growing list of stakeholder requirements and an explosion in creative solutions, we expect the mining industry to accelerate its adoption of technology.
The sense of urgency will grow as corporates pursue net-zero CO2 pledges, improved water management, continued improvements to employee safety, and cost optimisation through operational efficiency.
We have reviewed five areas of the production process that are seeing new – and not so new – technologies emerge. We believe that, in combination, they have the potential to materially improve the efficiency and sustainability of operating and financing copper assets.
1. Diesel displacement
Climate change and industry’s role in decarbonisation is rising to the top of agendas among investors and producers. With increasing requirements for environmental and emissions reporting, companies will be scrutinised for a lack of commitment to reducing carbon emissions.
We expect electrification trends to accelerate over the next decade.
Diesel consumption frequently contributes most of a mine site’s Scope 1 (direct) carbon emissions. Initiatives to displace diesel consumption are already underway at several operations. These include the increased electrification of mining fleets and adoption of conveyors.
We expect electrification trends to accelerate over the next decade. Progress is being made with underground mining equipment and battery-electric vehicles. Considering the battery capacity needed to power a 500-tonne loaded haul truck, however, a full battery-electric open pit haul truck seems like a distant proposition. But by harnessing established engineering, such as regenerative braking, trolley lines or even contactless charging on haul roads, could this be closer than we think?
Explore emissions risk with our interactive Emissions Benchmarking Tool.
2. Digitalisation
Sensors, equipment interconnectivity, remote operation centres, autonomous haulage and real-time monitoring systems are becoming increasingly common at modern mine sites.
Disruption and the need for workers to socially distance due to the coronavirus pandemic could accelerate the transition to remote working and automation.
Challenges to adoption are likely to be centred around capital investment requirements to establish new regimes and union engagement around job reduction, retraining and upskilling.
3. Electricity sourcing and generation
Several operators have entered into renewable power supply agreements this year. The most significant moves we have observed are taking place in Chile, where renewables play a prominent and growing role in the national electricity mix.
These changes will greatly reduce Scope 2 (indirect) carbon emissions in the next two to three years at several major copper mines, including Zaldivar, Centinela, Escondida Andacollo and the Quebrada Blanca mill project.
On-site self-generation, mostly using solar photovoltaic (PV) plants, has seen limited adoption in copper but is slowly growing with regular project additions.
Regenerative conveyance has been in place for some time at several sites in the Andes to use altitude differences across sites to harness gravitational potential from ore. El Abra, Collahuasi, Radomiro Tomic, Los Pelambres and Antapaccay currently use these systems, resulting in site reductions in net electricity demand of 5-10%.
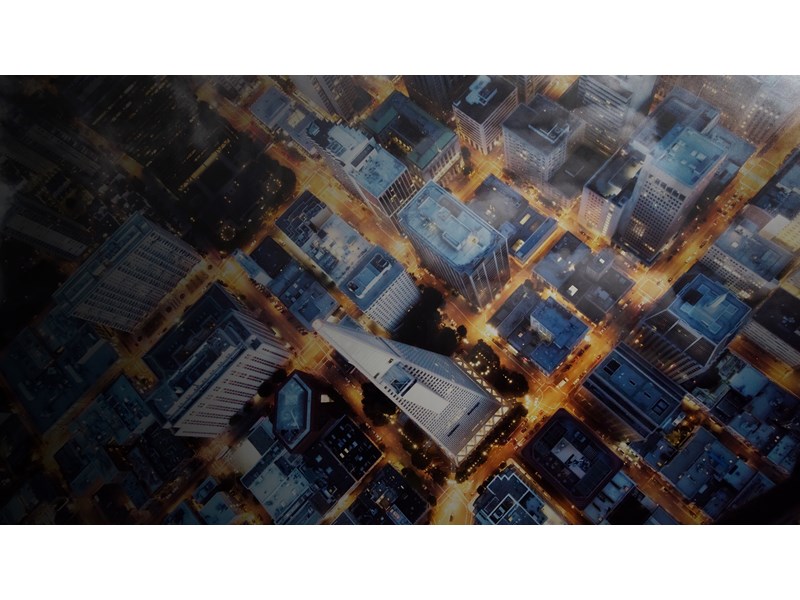
4. Gangue rejection and pre-concentration
Efforts at the mine to handle as much valuable mineral and as little waste rock as possible is an approach that can be broadly classified as gangue rejection. This strategy ensures that a higher proportion of payable ore and a lower proportion of barren rock is sent to the plant for processing.
Production geology and survey teams spend considerable time and effort to map ore and waste locations to inform production teams and minimise ore dilution. Such efforts can be negated by the irregular translation of ore and waste as it moves during blasting.
The growing reliance on the deployment and modelling of 3D sensor movement throughout the flitch being blasted – as opposed to manually tracking surface markers – is improving understanding and lowering the error margin of ore production activities.
Deployment of this technology has primarily been targeted at gold operations but is seeing application to other commodities, including copper, where high grade ore is present in tightly defined mineralised zones.
5. Advances in comminution and flotation
A significant limitation in the production of sulphide flotation concentrates has been an inability to reliably separate ore and waste in coarser particle sizes with conventional froth flotation. Consequently, additional costs are incurred – such as energy, water and grinding media – to grind the bulk of ore into very fine fractions (less than 30 microns) to recover metal sulphides and reject waste in the flotation cell.
Advances in equipment and reagents focus on pursuing flotation of more ore with grain sizes up to a millimetre scale and operating at considerably higher pulp density, therefore reducing energy and water requirements per tonne of ore processed and de-risking tailings management.
Find out more
Find out how to access our latest copper research, or explore emissions risk with our interactive Emissions Benchmarking Tool.