The future of automotive industry polymer demand
What does the rapid evolution in vehicles’ material composition mean for plastics
4 minute read
Sandheep Sebastian
Principal Data Scientist
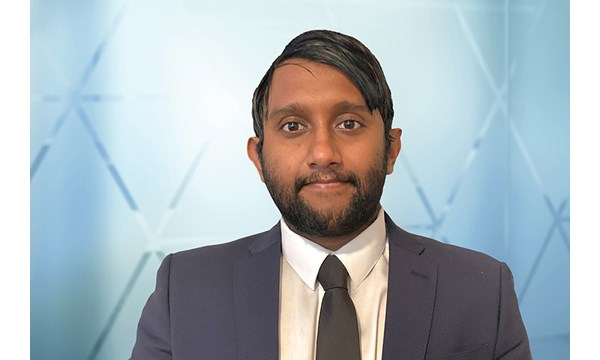
Sandheep Sebastian
Principal Data Scientist
Sandheep brings 10 years of experience as a Principal Data Scientist working in the Polymer Demand team.
Latest articles by Sandheep
-
Opinion
Plastic demand could reduce by up to 30% in an accelerated energy transition scenario
-
Opinion
Plastic demand: sectoral overview
-
Opinion
Why the world needs global rules on polymer use
-
Opinion
The future of automotive industry polymer demand
-
Opinion
Polymer demand scenarios: a little more conversation, a little less plastic
Rob Gilfillan
Head of Polymer & Fibres
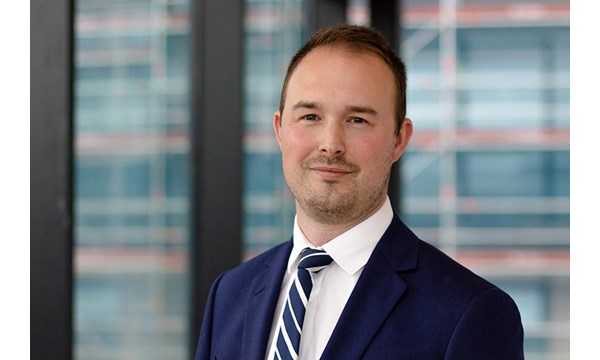
Rob Gilfillan
Head of Polymer & Fibres
Rob leads our research into regional and global markets for fibres, films and flexible packaging.
Latest articles by Rob
-
Featured
Oils & chemicals 2025 outlook
-
Opinion
Plastic demand could reduce by up to 30% in an accelerated energy transition scenario
-
Opinion
Plastic demand: sectoral overview
-
Opinion
The future of automotive industry polymer demand
-
Opinion
Polymer demand scenarios: a little more conversation, a little less plastic
-
Featured
Global challenges weigh on downstream chemical markets in 2023
Quentin De Carvalho
Head of Nylon / Polyamide
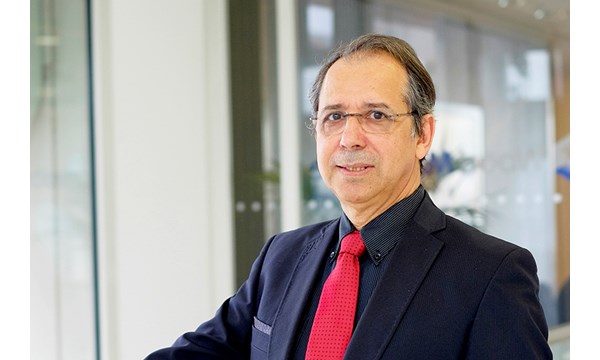
Quentin De Carvalho
Head of Nylon / Polyamide
Quentin has over 30 years’ experience in the chemical industry with a focus on polyamide nylon.
Latest articles by Quentin
-
Opinion
The future of automotive industry polymer demand
-
Opinion
The calm before the storm for the nylon industry?
The automotive industry is a large sector for polymer consumption globally, but with vehicle manufacturing undergoing significant change driven by new technology and consumer behaviour, what are the implications for increasing or decreasing use of plastics?
Our recently published insight Polymer demand trends in the transport sector uses Wood Mackenzie’s Material Applications Platform (MAP) to model the impact of key drivers on future plastics demand in the automotive sector. Fill out the form to get complimentary access to an exert from the report, or read on for a brief introduction.
What does the automotive sector use polymers for?
Plastics are used for a wide range of components in passenger vehicles, from interior fittings such as seats, door panels, dashboards, instrument clusters, carpets and airbags, to external items such as bumpers, lights, door handles and tyres. However, new technology and changing consumer behaviour are driving rapid change in vehicle manufacturing, with both positive and negative implications on the demand for polymers.
What’s driving increased polymer demand in the automotive sector?
The key drivers of increased demand for plastics in car manufacturing are the linked themes of electrification and lightweighting. Regional sustainability initiatives are incentivising the transition to new energy vehicles, particularly electric vehicles (EVs). By 2040, we forecast that battery electric vehicles (BEVs) and plug-in hybrid electric vehicles (PHEVs) will account for 60% of global passenger vehicle production.
The batteries used in EVs create a significant weight penalty – currently, an average medium sized battery electric vehicle is nearly 37% heavier than its traditional combustion engine equivalent. Higher weight translates to lower fuel efficiency, so car manufacturers are increasingly turning to lighter alternatives to steel such as aluminium and polymer composites to offset the problem.
What are the challenges to automotive polymer demand?
While the long-term trend towards electric vehicles is driving increased polymer demand, it’s not the only factor in play. Firstly, despite legislation and government policy aimed at pushing the transition to carbon neutral vehicles, there are risks to electrification. Currently, manufacturers are scaling back plans to build more EVs due to lower than expected sales, with consumers concerned about charger availability and high prices. Secondly, in the long term, overall passenger vehicle production is likely to decline as public transit and shared vehicle pool services reduce levels of private car ownership.
In time the trend towards electrification should recover. However, as the transition to a more sustainable economy progresses, a new factor will impact virgin polymer demand: recycling. The US Environmental Protection Agency estimates around 75% of a vehicle is recycled at the end of its life, but most of the plastic components are currently disposed of in landfills. In the future, government initiatives to design vehicles with component recovery in mind will mandate the use of recycled plastic content. This will increasingly direct plastics back into the value chain, reducing overall virgin polymer demand. At the same time, a more sustainably focused approach could encourage the use of specific polymers with high recyclability such as polypropylene.
How will an accelerated sustainability scenario impact auto industry polymer demand?
We used our proprietary Material Applications Platform to model the potential impact of accelerating electrification, lightweighting and recycling on polymer demand in the auto sector across five separate regions: Asia Ex-China, China, Europe, North America and the Rest of the World.
- Electrification scores assess the impact of emissions targets, legislation and incentives on the potential rate of EV adoption.
- Lightweighting scores evaluate the trend for using plastics in place of other materials for EV components to offset their heavier weight.
- Recycling scores are calculated based on the expected regional impact of legislative mandates and recycled content targets on auto industry demand for specific virgin polymers
Note that Europe’s electrification score stands out due to its 2030 carbon emission targets. China also scores well on electrification thanks to having provided credits for new energy vehicles since 2018 and exporting EVs to carbon-stringent countries.
Under our base case, polymer demand into passenger vehicles is expected to increase at 3% per year, rising from 20 million tonnes in 2023 to 34 million tonnes in 2040. This modest growth rate is based on the projected increase in vehicle production globally, independent of the drivetrain used.
Our accelerated sustainability scenario predicts an additional increase of 7% in overall polymer demand by 2040 over our base case, thanks to the impact of electrification and lightweighting. However, it also forecasts a 6% reduction in virgin polymer demand over the same period due to the impact of recycling (see chart below).
Trends for lightweighting and electrification of vehicles should be particularly beneficial to producers of polyamide and polypropylene. For fibres, polyester is expected to retain its cost advantage over nylon; producers can look at areas such as airbags, and the number per vehicle, for growth potential.
Don’t forget to fill in the form at the top of the page to download your complimentary extract from the report. This offers deeper analysis of the major drivers of polymer and fibre demand into passenger vehicles, including a range of charts and supporting data.