Coronavirus to disrupt China’s chemicals sector more than SARS
While the 2003 SARS outbreak hit during an economic supercycle, Covid-19 is set against a less favourable economic backdrop
2 minute read
Kelly Cui
Principal Analyst, Petrochemicals

Kelly Cui
Principal Analyst, Petrochemicals
Kelly is an expert in the coal-to-olefins (CTO) and methanol-to-olefins (MTO) sector.
Latest articles by Kelly
-
Opinion
Which global steam crackers are at most risk of closure?
-
The Edge
Big Oil’s opportunity for M&A in the petrochemicals downturn
-
Opinion
Why crude-to-chemicals is the obvious way forward
-
Opinion
Coronavirus to disrupt China’s chemicals sector more than SARS
-
Opinion
Can China’s CTO and MTO industries survive the threat of massive steam cracker investment?
-
Editorial
Why is China the early adopter of CTO/MTO
Coronavirus is not the first time that China’s economy has had to deal with the impact of a virus outbreak – SARS (severe acute respiratory syndrome) caused significant disruption in 2003. However, we expect the current outbreak to have a bigger impact, and have a more challenging road to recovery.
Here’s how the coronavirus outbreak differs, and how that affects China’s petrochemicals sector.
SARS hit during an economic supercycle
China was in the upper trend of an economic supercycle when the SARS epidemic hit, which mitigated its impact. Nonetheless, its economy was put under pressure in the first two quarters of the year, with sales of consumer goods taking a significant hit.
This dented olefins and polyolefins activity, with weak demand hitting all sectors – apart from medical hygiene applications. Convertors took time to recover. Some had to lower operating rates as domestic demand dipped, curtailing their margins. At the same time, exports dampened – overseas buyers were reluctant to take cargoes from China. This weighed on market prices.
The effect was much less apparent for aromatics. Most sectors along China’s polyester chain were growing rapidly in the upper trend of the business cycle, before and after the epidemic. In 2003, polyester polymer production increased by an impressive 22%.
Overall, the seasonal lull for chemicals in early 2003 extended into Q2 and utilisation was dented. But the market quickly bounced back and production clustered in the second half of the year.
Coronavirus is set against a very different economic backdrop
Today, the economic landscape is much less favourable. China’s economic engine has been cooling, and downward pressure increased with the trade war with the US. What’s more, the coronavirus is hitting harder than SARS did. It has a higher rate of contagion, and many cities are still restricting the movement of people and goods in response.
This will take its toll on demand in the same way that SARS did in 2003. Sales of consumer goods will bounce back in the same way too, once the epidemic passes, but given the economic landscape the dent it leaves may be deeper.
The extended holiday period amplified the disruption
Sluggish demand from end-use plants and restricted transportation are now forcing upstream feedstock plants to lower their operating rates. Sinopec-SK Wuhan Petrochemical has lowered the operating rate of its 800 kta cracker by 10%. A 300 kta cracker expansion, scheduled for completion in July, will also be delayed.
The holiday period has been a factor too. Some producers started maintenance before the Chinese New Year holiday and extended their downtime when local governments prolonged the holiday to limit the spread of the virus. Other running plants may reduce runs or slate stoppages, due to high product inventory and delays in feedstock transportation. Meanwhile, cancelled flights and train journeys, and even blockades on some highways, have grounded workers in their hometowns.
Transport restrictions and the extended holiday period are likely to delay the start-up of projects scheduled for H2 2020. We estimate around 2-3 months’ delay in the olefins sector.
The effect will be felt across the value chain
Demand for chemicals in China typically dips during the New Year holiday period. The coronavirus outbreak will prolong this, affecting all stages of the chemicals value chain.
For example, as retail activity drops – and the consumption of commodities and disposable packaging drops with it – demand for polyolefins will decrease. Polyester producers are also feeling the pressure. Feedstock price slump has hit fibre and bottle chip producers’ margins, and those who produced over the holiday could see inventory accumulate due to weak demand.
Read more about the impact of the coronavirus on the Chinese polyester industry.
There are some (small) exceptions. Demand for surgical face masks, used to prevent the spread of infection, has pulled up fibre polypropylene demand. China produced 5 billion masks in 2019 and we expect this to increase by at least 30% in 2020. However, as only 4 grams of polypropylene fibre is needed to produce a mask, the effect is limited.
So, when will recovery start?
The duration and severity of the outbreak remain to be seen. Transport restrictions are the main limit on the pace of recovery – once lifted, plants can gradually resume normal production and outflow. We expect that these restrictions will be lifted in March – paving the way for the market to start to recover from Q2.
Find out more
As part of our recent webinar 'Coronavirus (Covid-19) Outbreak: impact on commodities', principal consultant Salmon Lee discussed how virus containment measures are affecting China’s oil and petrochemicals demand.
This included charts on:
- The impact on China's oil demand;
- Polyester production: base case outlook and downside case;
- Polyester fibres: base case outlook and downside case;
- Price outlook: chemicals feedstock.
Fill in the form at the top of this page for a complimentary copy of the presentation slides.
The Chemical Reaction
Read the latest news and views from our chemicals experts around the world. Recent stories have included:
- The coronavirus and its impact on the polyester chain
- Signs of stress or just moving on? Announcements by chlor-vinyls players beg the question
- China's polyester giant Zhejiang Petrochemical starts up 1.4 Mtpa cracker
Visit our store to find out more about the Chemical Reaction.
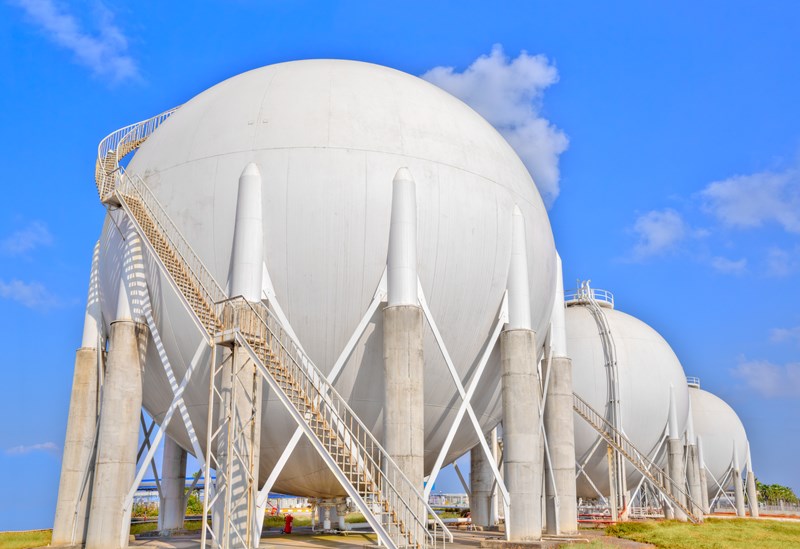
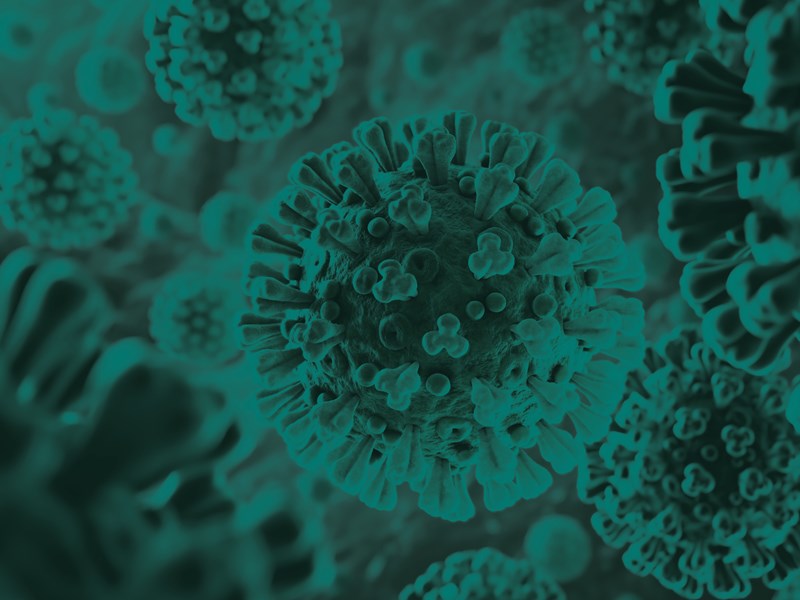