Is the energy transition road paved with scrap metal?
Scrap could help to decarbonise the metals and mining industry, and fill a looming supply gap – but policy change will be crucial
1 minute read
Julian Kettle
Senior Vice President, Vice Chair Metals and Mining
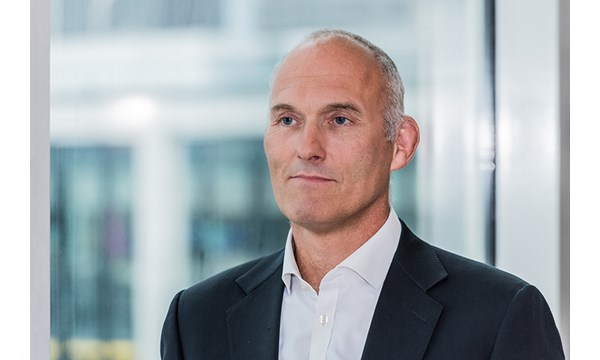
Julian Kettle
Senior Vice President, Vice Chair Metals and Mining
Latest articles by Julian
-
Opinion
Metals investment: the darkest hour is just before the dawn
-
Opinion
Ebook | How can the Super Region enable the energy transition?
-
The Edge
Can battery innovation accelerate the energy transition?
-
Featured
Have miners missed the boat to invest and get ahead of the energy transition?
-
Featured
Why the energy transition will be powered by metals
-
Featured
Could Big Energy and miners join forces to deliver a faster transition?
Metals will play a starring role in the energy transition. Five key metals – aluminium, cobalt, copper, nickel and lithium – will play a vital role in the transformational switch towards a greener energy future, as key components in electric vehicles, battery energy storage, wind and solar technology and electricity transmission.
The metals and mining industry will need major investment of over US$1 trillion in the next 15 years if it is to satisfy the material needs of an accelerated energy transition which limits the average global temperature increase to 2° C by 2050 – our AET-2 scenario. This amount is in addition to investment required under our base case, which assumes temperatures rise to no more than 3° C.
And securing that investment will only be the start of the challenge. If the industry sticks to existing production methods, meeting increased demand would add 12 billion tonnes of carbon to the value chain by 2040.
Without economic, timely, reliable and sustainable metal supply, the pace of the energy transition will be inhibited. But scrap could provide a solution – provided the right incentives are in place.
Using scrap will reduce emissions significantly
Primary steel and aluminium production processes are energy and emissions-intensive: the steel industry is responsible for close to 10% of global emissions, while aluminium produces roughly 2%.
Increasing the use of scrap is the first logical step on the road to decarbonisation. But it requires a massive ramp-up in green energy supply and investment in collection infrastructure.
We estimate that using all available scrap could reduce aluminium and steelmaking emissions by somewhere between 300Mt and 800Mt a year each – depending on the region and technology. And in an accelerated energy transition scenario, where the carbon price per tonne could increase to US$110, maximising scrap use could translate to significant savings in carbon taxes of up to US$85 billion for steel and US$37 billion for aluminium per annum.
Scrap is significantly less capital intensive
Another drawcard for scrap is that less capital is needed to install a scrap smelting plant than to establish a primary facility. However, some investment will still be needed.
For steel, we estimate that the total capex required to absorb all additional scrap would come to around half a trillion dollars. A huge amount for an industry already under financial pressure.
In the world where all available scrap is used, secondary scrap processing capacity for aluminium would need a near threefold increase on what we have today, at a cost of around US$15 billion. While that’s a fraction of the investment needed for steel, it’s still a very significant sum and won’t happen without significant stimulus.
Without stronger policy incentives, scrap use will be limited
Although there’s a strong economic rationale for greater scrap processing and use, it will remain underused until clearer incentives are introduced.
Stricter environmental policies could change that. Carbon tax policy is likely to accelerate scrap processing. And consumer or investor pressure to increase recycled content could transform the market – but that won’t happen overnight. Improvements need to be made to the collection and recycling process to address fragmented collection infrastructure, which in turn will require investment.
Will we need to mine metals in the future?
In a recent report we delved deeper into the implications of increased scrap use for the metals and mining industry, and discussed:
- How much additional scrap could be made available?
- If all available scrap is recovered, is it possible to eliminate the need for the mining and processing of primary metal?
- Will metal prices drive future scrap use?
Fill in the form at the top of the page to readthe report in full.