Discuss your challenges with our solutions experts
How to manage renewables supply chain issues
Developers need to manage an increasingly complex array of factors to ensure project success
8 minute read
Erin Carroll
Senior Vice President, Supply Chain Consulting
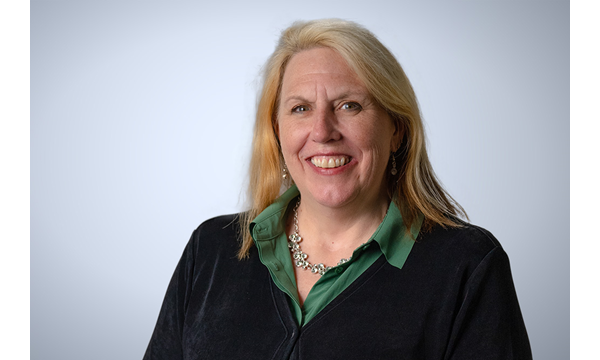
Erin Carroll
Senior Vice President, Supply Chain Consulting
Latest articles by Erin
-
Opinion
How to choose the right renewables project model
-
Opinion
Factors to consider when choosing OEMs for renewables projects
-
Opinion
How does the Inflation Reduction Act impact renewables project planning?
-
Opinion
How to manage renewables supply chain issues
Globally, renewables supply chains are impacted by many of the same issues affecting other industries. However, in the US, supply-demand imbalances in key raw materials and components for renewables projects are being exacerbated by the Federal Government’s dual carrot-and-stick approach to boosting the domestic renewables sector.
The supportive environment provided by the Inflation Reduction Act (IRA) is creating a healthy project pipeline for renewables in the US. But while the IRA also incentivises domestic equipment manufacturing for renewables, the scaling up of supply is inevitably lagging the increase in demand. At the same time, controls and levies on imported equipment such as solar panels, wind turbines and storage batteries are impacting the viability of sourcing components from abroad.
To make informed project planning decisions, developers and owners need to understand the complex interplay of these factors.
Renewables raw materials costs
Currently, most raw materials used in US renewables projects are imported – particularly the polysilicon for making solar panels and the lithium used in large-scale batteries for energy storage. China dominates supply chains for key renewables materials, accounting for almost 90% of global polysilicon supply in 2023, projected to reach to 94% in 2024, while upwards of 70% of global lithium refining capacity is based in China. This highlights the lack of domestic supply chains in the renewables space, with the US accounting for 3% of global polysilicon production and 2% of lithium refining.
Lithium and polysilicon prices have undergone extreme volatility since the onset of the pandemic. Lithium carbonate and hydroxide reached all-time highs in December 2022 before tumbling in 2023 amid weakening sentiment from the EV sector with prices falling to their lowest level since 2021 in Q1 2024. For polysilicon, prices sat around long-term highs for much of the second half of 2022, before a combination of project delays and ballooning manufacturing capacity saw prices drop to their lowest level since
Meanwhile, the cost of other key commodities, including steel and copper, are still above pre-pandemic levels despite recent economic headwinds with bullish price sentiment expected in the second half of 2024.
Regulatory issues
Issues relating to two key regulations are having a strong impact on the supply chain for US renewables.
Firstly, attempts by foreign companies to dodge US tariffs on Chinese imports and evade US Anti-dumping and Countervailing Duty orders have led to significant bottlenecks in the solar supply chain. Following complaints by US solar manufacturers, a Department of Commerce investigation found companies were breaching regulations by shipping Chinese components to Cambodia, Malaysia, Thailand and Vietnam for assembly, before sending them on to the US. As a result, all companies in these countries must now certify they are not trying to evade import duties.
Secondly, the Uyghur Forced Labor Prevention Act (UFLPA) prohibits the importation of goods produced in the Xinjiang region of China, absent proof that forced labour has not been involved in their manufacture. Unfortunately, tracking the origin of polysilicon is difficult and the validation process is not fully vetted, resulting in solar modules being held at import facilities while investigations are carried out. The first modules manufactured using non-Xinjiang Chinese polysilicon were released into the US in November 2023, although a bulk of module imports to the US are still coming from Southeast Asian countries.
As well as preventing illegal imports, these rules create red tape and resultant delays for legitimate imports. In the short term this is restricting the supply of vital materials and components, delaying projects and pushing up costs.
Other potential risks to the US solar sector include the recently imposed import duties on aluminum extrusions from China, Indonesia, Mexico and Turkey, which could include aluminum solar racking systems and module frames.
Domestic content
At the same time as providing tax incentives to encourage investment in renewables projects, the IRA aims to boost US manufacturing through additional tax credits for projects built using a high percentage of domestic content. However, recently issued guidance from the IRS on domestic content requirements is complex and burdensome.
The existing US supply chain gives onshore and offshore wind projects a reasonable chance of meeting definitions for domestic content. But for solar the situation is more challenging, since even when elements such as solar modules are manufactured in the US, components often come from abroad.
While domestic manufacturing for solar is underway, the US market for mono and polysilicon panels is still developing. The existing US firms will lack the ability to manufacture polysilicon solar cells until the end of the decade. High-efficiency mono perc solar modules use imported cells which account for 70% of their cost, so projects will struggle to meet the required standards for domestic content. Without the benefit of the additional tax credit, domestic modules are noticeably more costly than their imported counterparts.
Battery systems face similar problems meeting domestic content requirements. Once again, while plans for domestic battery manufacturing have been announced, most battery packs are still imported from overseas. Given these issues, the US Government is walking a fine line between spurring domestic manufacturing capacity and contributing to project delays and even curtailment.
Project pipeline and labour supply
Another short-term issue has been created by the backlog of projects that were standing ready to go pending implementation of the IRA. With these projects now being greenlighted, the market is experiencing a surge in demand for both equipment and labour that threatens to cause further delays.
Adding to the labour issue is the fact that the IRA offers additional tax credits for prevailing wage and apprenticeship programmes. That means contractors with qualifying programmes can demand higher prices, while those compelled to introduce the necessary infrastructure or raise wages face higher costs. In the short term this is driving price inflation.
Interconnection and permitting
The list of interconnection requirements, approvals and permits needed for power projects creates a further potential bottleneck, as well as adding significantly to costs (interconnection fees can be prohibitively high). Waiting times for interconnection permit approvals run into years in some regional jurisdictions, with projects in interconnection queues comfortably exceeding projected builds in most regions (see chart below).
Key equipment supply
A final issue to be aware of concerns the step-up transformers which are vital for connecting power projects including solar systems to the grid. Increased demand from renewables projects means delivery timescales currently range from 1-2 years for distribution voltage and smaller step-up transformers up to 3-5 years for larger generator step-up transformers (GSUs) and power transformers.
Four golden rules for managing renewable supply chain issues
While surety of supply has always been a key issue in project management, this complicated array of factors means developers and owners need to plan more carefully than ever. This applies both to individual projects and in terms of managing project portfolios to make best use of available resources. We suggest four key rules to minimise problems deriving from supply chain issues.
1. Plan early
Developers should make use of their previous experience, but also need to benchmark assumptions against current market conditions.
- Planning should be proactive not reactive, starting as early as possible in the life of the project
- Long lead times mean supply chains for key components should be considered from the outset
- Don’t assume lead times factored in for past projects will apply in the current market
- Pulse the market regularly to avoid being caught out by emerging supply issues and delays
2. Carry out due diligence on suppliers
Where previously due diligence focused on component cost, potential importation issues and suppliers’ ability to meet project capacity, now domestic content is a key issue.
- The IRA makes domestic manufacturers potentially highly desirable from a cost standpoint, but suppliers must be able to deliver at the scale and in the timeframe required
- Partnering with a domestic supplier by offering a guaranteed order may help them scale rapidly while improving surety that needs will be met
- Be proactive in terms of understanding timescales for manufacture and factoring into your project planning
- The risk of delay or curtailment should be carefully assessed, since this will impact not only the cost but the viability of the project
3. Be conscience of overall project schedules
Timescales for all aspects of a project need to be considered holistically rather than individually.
- Assess the potential knock-on effect of delays in the delivery of core components, the construction of key elements, the provision of permits and interconnection to the grid
- For energy storage projects, batteries start to degrade as soon as they are manufactured – any delay to your project after delivery could therefore curtail the working lifespan of batteries
- Be aware that delays can fall under force majeure clauses in contracts; for example, regulatory changes
4. Keep your options open
Managing risk effectively means ensuring a degree of optionality and flexibility in your planning.
- Avoid putting all your eggs in one basket by having both primary and secondary options in place for the supply of key components
- Create get-out clauses in contracts so you have offramps if suppliers fail to deliver
- For multiple projects consider using more than one supplier; this may give you the option to mix across projects or scale up supply from one manufacturer if there are issues with the other; however, bear in mind that there may be cost impacts to this approach that need to be evaluated in the context of when the project output is required
- Carefully evaluate if the domestic content bonus makes economic sense for your project; the cost of meeting domestic content requirements may exceed the financial benefit of the tax credit bonus
Given the range of factors involved, managing the supply chain for renewables projects effectively is increasingly challenging. Wood Mackenzie’s Supply Chain Intelligence team have significant sector-specific experience and access to a wide range of proprietary data to help you in making the right decisions.
Learn more
Find out more about the insight and analysis available from Supply Chain Intelligence by filling out the form at the top of the page.
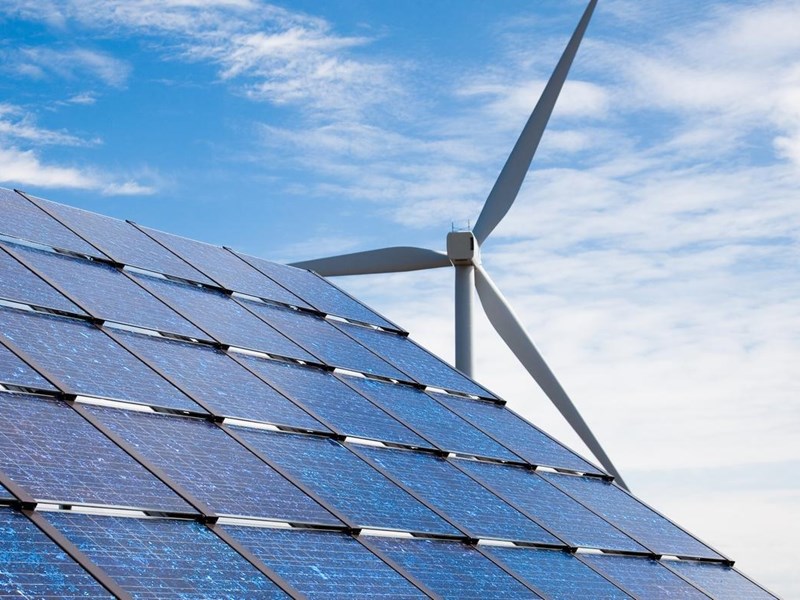